Carpet technique and history
The carpet was initially born with the purpose of protecting against the cold but, with the passage of time, it became, especially from the sixteenth century, a real art with a very high degree of specialization and sophistication.
Today, he is one of the greatest exponents of Eastern art and culture, especially Persian.
HISTORY
The oldest carpet that is preserved so far is “the Pazyryk carpet” found in 1949 in the Pazyryk Valley, Siberia by the Russian archaeologist Rudenko and dating from the fifth century B.C. so it is approximately 2,500 years old , although its high degree of technical perfection suggests the need for at least ten centuries of evolution in carpet weaving to reach that point. Therefore , we can conclude that carpet weaving has its beginnings at least 3500 years ago.
With the exception of the Pazyryk carpet, few other pieces are preserved from ancient times and periods, we only have written documentation that mentions them.
They began to be imported to Europe in the thirteenth century as reflected in some paintings of that time.
The carpet industry, as such, was born in Persia in the Safavid period and it is, from that moment, that they began to be exported to areas adjacent to Persia and further and further away, until they reached Europe.
The first workshops can be found in cities such as Isfahan, Kashan and Kirman, which produced carpets for both the nobility and private citizens, always on request. This boost to the carpet industry is due, to a large extent, to the interest of the Safavid monarchs in this art. After this dynasty came the Qajar (1797) which continued to foster and support this flourishing industry.

Pazyryk Rug

Ziegler Rug
It is from the second half of the nineteenth century when Persian carpets begin to be massively exported to Europe , especially in Great Britain, there were even two British companies that came to have manufactures in Iran, (Ziegler and Hotz), as well as France and the United States.
It was at the end of the Qajar period that artificial dyes were first introduced in Iran, which the government banned in 1877.
So we come to the period of the two world wars that represented a significant decline of this industry, resuming production from 1948 thanks to the patronage of the Pahlavi dynasty. In 1949 the government of the Shah organized a conference in order to deal with the problems that afflicted the Persian carpet (use of artificial dyes, decrease in the quality of both materials and the technique used…) and it is from this conference that a series of laws and measures were introduced that led to an important resurgence of this art with the production of carpets of the highest quality.
We come to the year 1978-1979 and the arrival of the Islamic Revolution, which brought such disastrous consequences both for the country and for the entire international community. Khomeini’s government drastically reduced the export of carpets to the West by considering them a “national treasure”, finally abandoning this policy in the mid-80s in the face of the importance and magnitude of the income it was giving up. It is from that moment on that exports increase significantly, which led to a decrease in the price of carpets worldwide.
Nowadays we are talking about an industry with good health and important production that is exported to the whole world, although the production of mechanical carpets is also of great importance, which are generally, although not always, cheaper although of much lower quality. Both products, mechanical and manual carpets, coexist although separated by an abyss when it comes to quality.
MANUFACTURING.
As far as manufacturing is concerned, we can distinguish a series of key themes:
1. The loom.
2. Carpet structure: weft and warp.
3. Knots.
4. Tools.
5. Raw materials.
6. Dyes.
1. THE LOOM.
Although there are different types of looms, two of them stand out:
* Vertical loom: This is, although a more rustic model with certain technical limitations, the most widespread either in its primary version or especially in the different models that have subsequently evolved from this first base. It consists of two vertical poles in parallel between which the plot extends. The weaver sits in front of a bench and, as the carpet progresses, that bench is raised upwards and continues to be woven until it reaches the top.
As we have said, from this vertical loom the most complete and sophisticated looms are developed that allow the creation of carpets of greater complexity.
* Horizontal Loom: It is the most rudimentary of them all and used mainly by nomadic tribes. They are two sticks, in this case, parallel horizontally between which the warps extend.

Vertical loom

Horizontal loom
2. CARPET STRUCTURE. (Weft and warp)
The structure or skeleton of a carpet is made up of a “mesh” where vertical and horizontal threads intersect. The vertical ones are called warp and the horizontal ones are called weft. Therefore, the fringes of a rug are the two ends of the warp, the thread that runs vertically through the rug.
The wool is knotted over the warp, that is, the knot is attached to the vertical threads. The horizontal ones, which are placed between two rows of knots, serve to tighten the knots well, stabilize them and, in this way, prevent them from moving.

3. KNOTS.
There are basically two types of knots:
* Ghiordes knot (also called Turkish or symmetrical) used mainly in Turkey, the Caucasus and some fairly large areas of Iran. Knot of great consistency and resistance.
* Senneh knot (also called Persian or asymmetrical) used mainly in Persia. It is usually used in thinner rugs as they take up less space. As a curiosity it should be noted that Senneh is an area of Iran where the Ghiordes or Turkish knot is used to weave carpets!
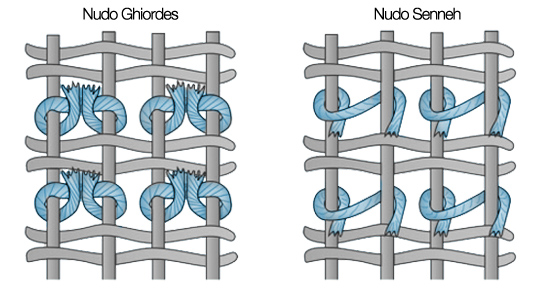
Looking at these two illustrations, the structure of each of them is perfectly understood.
Hispano-Arabic style carpet knot
It is interesting to note that in the hand-woven carpets in Spain, a knotting technique of their own is used, which gives rise to the so-called “Hispano-Arab knot”.
The fundamental characteristic is that the knot is attached to a single warp, unlike the previous two which, in both cases, each knot is attached to two warps.

4. TOOLS.
There are not many of them and they have some very basic characteristics:
– The knife to cut the knotted wool.
– The comb is used to hit the knots already made and, in this way, tighten them more to the weft.
– The scissors are used to cut the excess wool from the knot and thus be able to level the height of the pile of the carpet.

Tools for making a carpet
5. RAW MATERIALS.
There are basically three: wool, silk and cotton.
While cotton is used almost exclusively for weft and warp, wool and silk are used interchangeably for carpet pile or for carpet structure, weft and warp.
The more knots the carpet has and the higher the quality, the finer the threads of its skeleton should be. Thus, the most rustic rugs (with a larger and coarser knot have a wool structure that is a thicker thread, the finer rugs have a cotton structure that allows us finer threads and finally the extra fine rugs or of more excellent quality use silk wefts and warps to be able to make smaller knots and that they are closer together.
On some occasions, especially in Nain, Isfahan, Tabriz, Ghom or Bidjar , the pile of the carpet is wool although with numerous flowers or lines made of silk.
6. DYES.
Basically, this is the process followed for the dyeing of wool or other materials:
First the wool is introduced into a “mordant” bath used to better fix the dye to the wool, so that the dyeing has greater stability and there are no problems later when we wash the carpet. Then, in another jar, the wool is dyed in a dye bath and finally the skeins of wool are left to dry in the sun.
Artificial dyes appeared at the end of the nineteenth century and, therefore, until that date all dyes were natural , which means that they have a vegetable, animal or mineral origin, in short, they come from some natural element in contrast to artificial dyes that come from a chemical process combining laboratory and industry.
Some of the most notable natural dyes are:
– Pellet root to obtain red.
– Indigo leaves to obtain the blue.
– Vine or saffron leaves to obtain yellow.
– By mixing blue and yellow we get the green color.
– White, grey and brown wool is generally undyed and comes from the natural colour of the animal , although sometimes walnut shells are used to obtain a brown or similar tone.
Nowadays artificial dyes are widespread in the world of carpets with an excellent result, since more important than using a natural dye is to achieve a correct dyeing of the wool and that the dye is correctly fixed in order to avoid later problems.